5S
5S is a systematic approach to optimizing the working environment. It supports productivity in a company by securing lasting cleanliness and order in all corporate divisions.
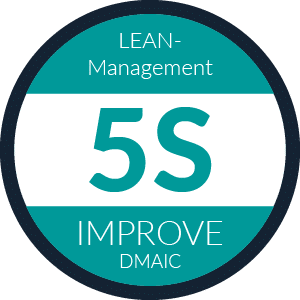
5S
5S is a systematic approach to optimizing the working environment. It supports productivity in a company by securing lasting cleanliness and order in all corporate divisions.
The 5S Cycle
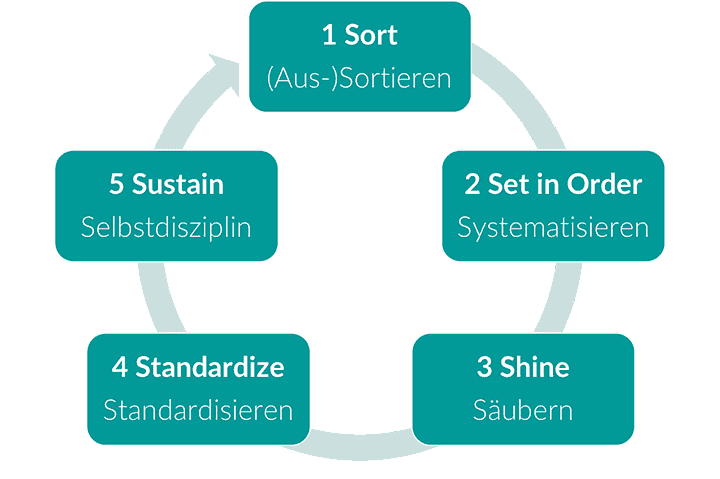
The name 5S is determined by the five steps beginning with the letter “S”, that are passed through in the application. 5S has the goal to improve security, quality and productivity of the work environment. Like many concepts of lean management, the 5S method also originates from the Toyota Production System.
The underlying cycle is built on sorting out, systemizing, cleaning, standardizing and self-discipline. Hereafter the individual steps are presented.
1 Sort
Goal Setting
In the sorting out stage, all materials and articles in the work environment that aren’t used or needed for everyday work are removed. The goal is to remove all unnecessary items from the work environment.
Approach
Initially all potentially unnecessary items are identified. For workplaces, machines and tools that are used by multiple persons, the red tagging method is recommended. Objects, that are classified as unnecessary by the employees, are marked with red tags. On these tags, employees can write, who and why they marked it (e.g. not used since:…, unnecessary). At the same time a deadline is set for the decision about the element. Depending on the work environment, recommendations go from two weeks to one month.
If no employee disagrees with the tag within the deadline, the elements are removed from the work environment. The element can be sold, scrapped or gifted to employees. If within the deadline an employee decides he wants to keep the item, employees can discuss about its possible remaining. If it is kept after all, the red tag is removed. Otherwise it will be transferred to a red tag area. This area is intended for useful but currently unnecessary items. There they can then be made available to other teams.
Alternatively red dots can be used. Here too a deadline is set, at the end of which a decision will be made. The tagging occurs with a red dot. If the items are used within the set deadline, the red dot is removed. The items that still have a red dot on them are removed from the work environment. Depending on the item, you can then later store, sell, rent it or offer scrap.
With both these methods the following maxim should apply: „When in doubt, throw it out“.
2 Set in Order
Goal Setting
The goal of the second step is to arrange and indicate all the needed items so that they have a permanent place. This ensures that everyone can find them and everyone can put them back to its right place.
Approach
For this step various helping tools can be useful. Shadow Boards, that show the outlines of the items, are popular for tools. In this way, the right place is clearly defined and a discrepancy immediately stands out. In this case, the principles of workplace ergonomics should be respected in order to achieve optimal results.
Furthermore colors and other tags could be useful for enabling a clear-cut identification. For example, all items on a workplace could be tagged with blue duct tape.
Especially in drawers, foam inserts can be a practical way to store the items in a nonslip and systematic manner. They are freely configurable and available at many different vendors.
3 Shine
Goal Setting
This step’s goal is to remove dirt from the work environment. Dirt can hide damages on the machines, which negatively impact the production and can even pose security risks.
An adequate cleanliness should thus be established in all corporate divisions. Of course the possibilities differ between a foundry and an office. Choose a realistic and accomplishable degree of cleanliness.
Approach
Initially it is important to establish extensive cleanliness. In order to achieve that, set an example and start by cleaning your workplace.
In the second step cleaning areas and their goals are set. On the basis of the goals and the expected dirt, schedules, processes and responsibilities are defined. At the same time audit objectives are defined. That should create a basis for a lasting cleanliness. Make before and after pictures in order to keep hold of the success of the cleaning action and to visualize the target state.
4 Standardize
Goal Setting
Goal setting is defining standards for the application of the first three steps. Standards make it easier to do things right at all times.
Approach
Here you should use the experiences you made in the first three phases. If in one area the use of certain methods have been very successful, they could be potential standards for the whole company.
Furthermore, 5S audit templates and checklists should also be created now to determine compliance and potential deviations.
5 Sustain
Goal Setting
To ensure that the previous efforts were not in vain, 5S must now be integrated into daily work and processes. Only then 5S can serve to significantly reduce search times and potential sources of accidents.
Approach
Now the previous steps should be maintained with self-discipline and clear rules. To this end, regular checks are carried out in which the standards from the fourth phase are examined.
In all phases of 5S, the involvement of each employee is extremely important. Only then does the necessary acceptance for the sustainable success of the actions emerge. Use this phase to ensure that all employees support 5S.
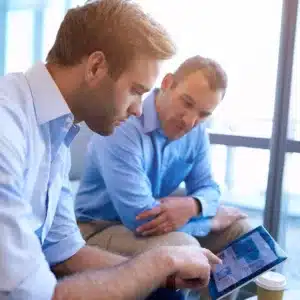
Do you have questions about implementing 5S?
Contact us – we are happy to discuss your questions on the topic with you, free of charge and without obligation.