Optimize transparency and performance of your manufacturing operations.
The Industrial IoT platform from Selfbits transforms your manufacturing data into insights and actions for continuous improvement. Powerful apps help you reduce machine downtime, increase throughput, and enhance the profitability of your machines and equipment.
As consultants, we support you in developing digital strategies in the field of Industry 4.0, implementing them with software solutions, and tackling your challenges in operations management.
What if you finally had good data for your important decisions?
Manufacturing companies are currently facing three key challenges:
How can we achieve more growth? How do we overcome the skilled labor shortage? And how do we manage the modern VUCA world?
At the same time, many companies lack a solid data foundation. Key production metrics are either unknown or difficult to obtain, delaying management decisions.
Selfbits helps you tackle these challenges. Our IoT specialists connect your machines and manual processes, creating a digital and networked production environment. This enables you to make informed investment, workforce, and pricing decisions based on reliable data. As a result, your company’s profitability and competitive strength increase.
Already more than
Recorded machine signals!
"With Selfbits, we have managed to centrally capture real-time telemetry data from our robots and provide it on web dashboards for our customers' analysis. The collaboration was always collaborative and trustful."
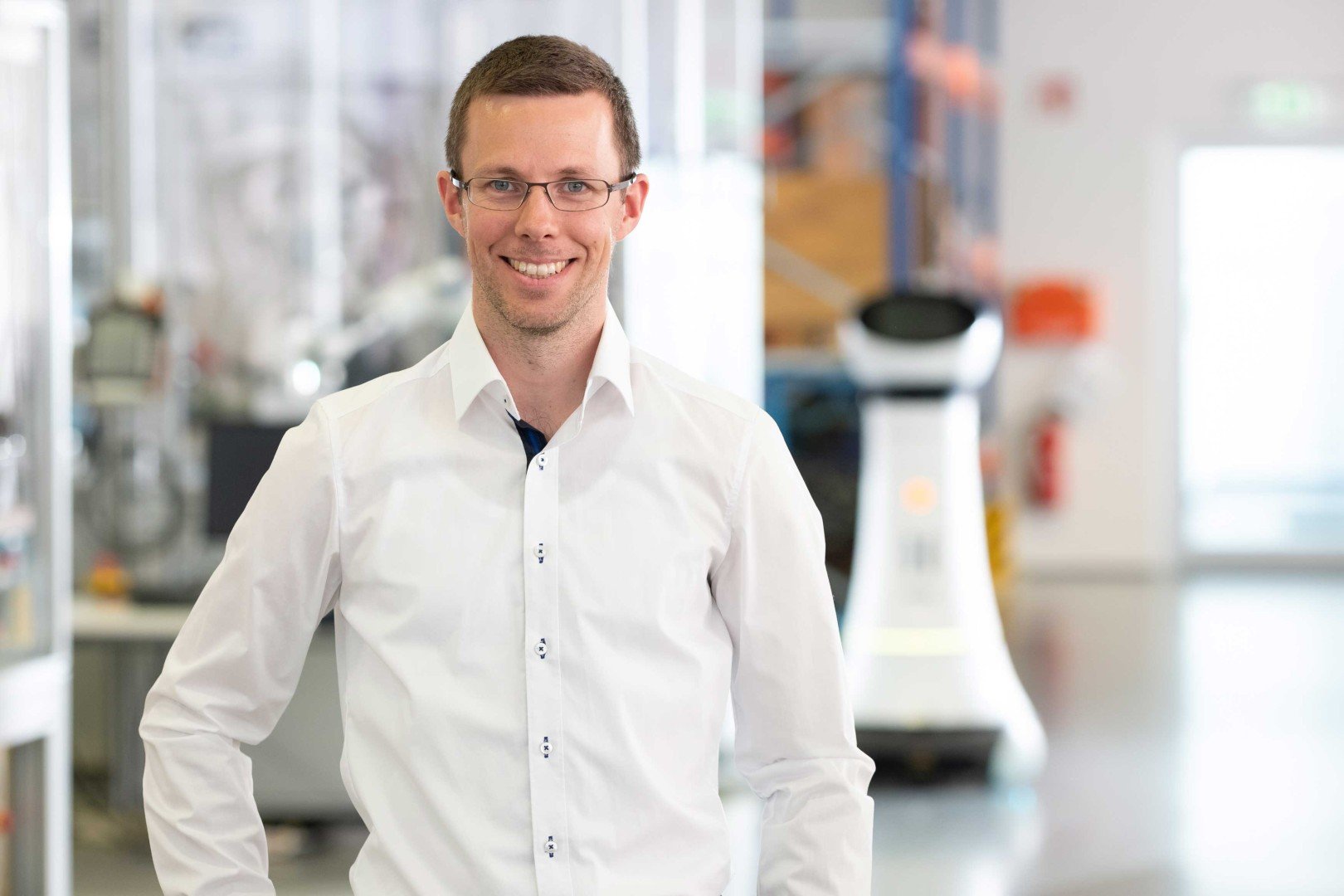
"By utilizing the Selfbits Manufacturing Suite, we were able to achieve much-needed real-time transparency on order progress, disruptions, scrap rates, and part whereabouts. Customer inquiries regarding order status can now be answered in real-time at any time."
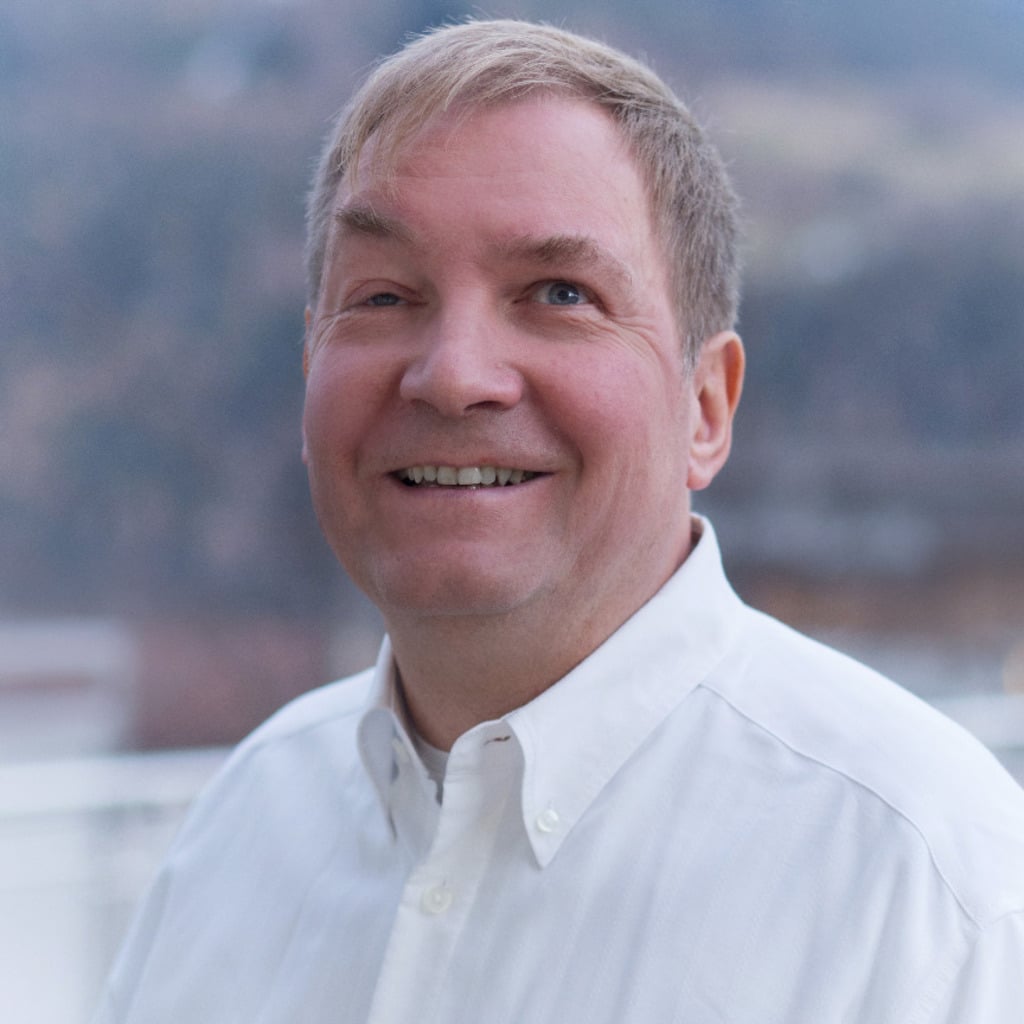
"Through a consistently rigorous and holistic approach, Selfbits has substantially supported us in leveling up our production area and created new perspectives for the comprehensive digitization of our industrial production processes."
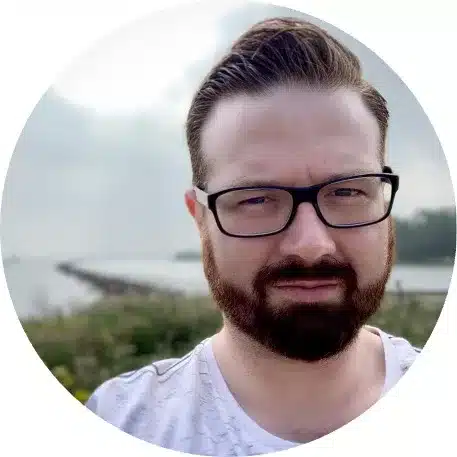
"Thanks to the Selfbits Manufacturing Suite, we have full transparency and control over our production from job preparation to shipment at all times."
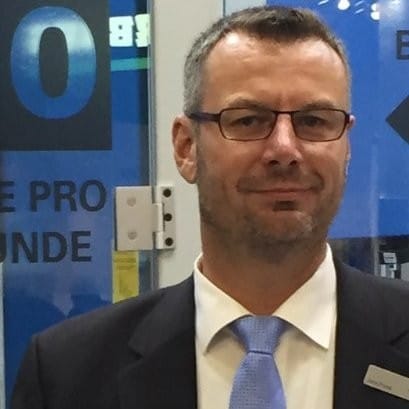
"In a very short time, Selfbits identified the main reasons for process inefficiencies in our production and ensured process data transparency, enabling us to quickly implement effective optimization measures."
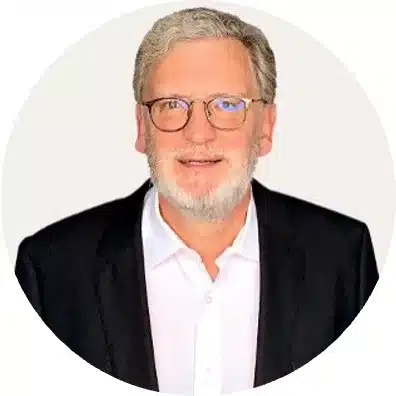
Achieve digital success like Karl Reichenbach GmbH!
“Selfbits has helped us create a fully paperless production. Most information is captured automatically through machine data acquisition.
The real-time transparency enables us to increase both our revenue and our profits.”
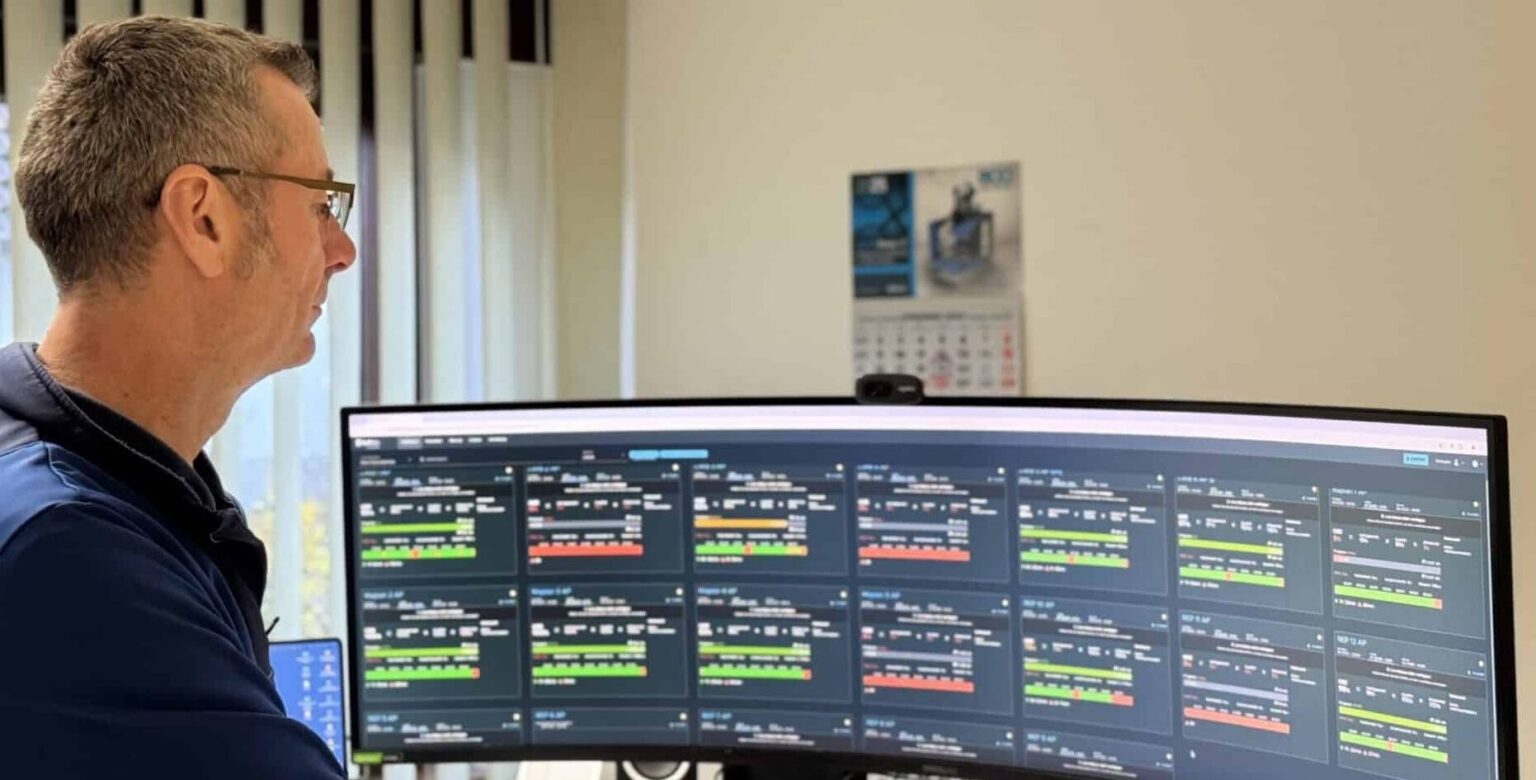
+300% efficiency gains in production planning
Get started now with these use cases:
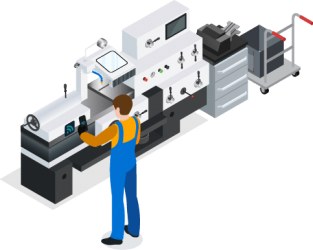
Real-time operational data acquisition
Use tablets at your machines and manual workstations to capture critical information in real time, right on-site.
Smart apps from Selfbits record key data such as quantities, good parts, rework and scrap parts, setup times, disruptions, downtimes, and their causes. Forms can be filled out easily and intuitively directly on-site with Selfbits.
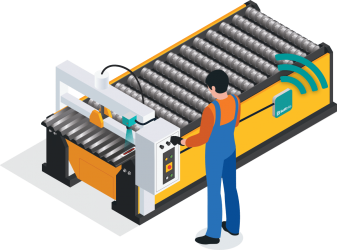
Machine data acquisition
Flexible hardware solutions from our IoT specialists help you capture your machine and sensor data with second-level precision, fully automated from your equipment. Your machines can be connected via OPC-UA or through retrofitted hardware and sensors.
Information is stored per item and order, ensuring that it is always available for your analyses and decision-making.
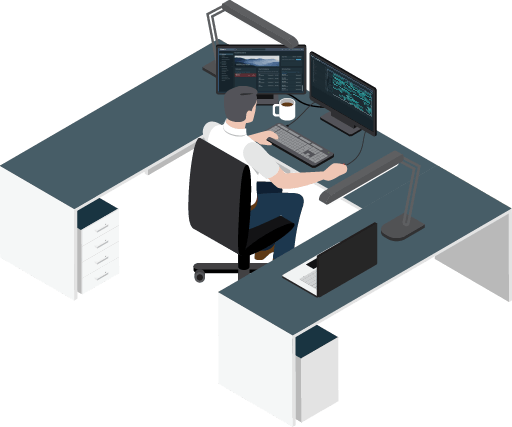
Digital production
With Selfbits, you always have a clear view of your production’s planned and actual status. Digitally map your manufacturing orders and use smart drag-and-drop planning tools:
Planning boards, capacity planning, order-specific progress monitoring, and more support your production planning and control. This enables you to manage production challenges flexibly and efficiently.
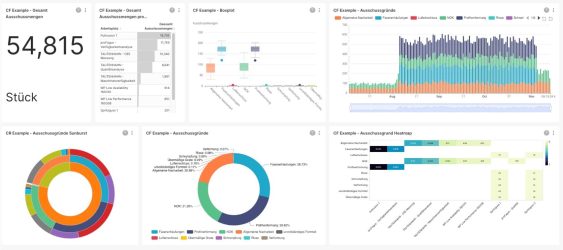
Digital KPI Management
Manage your production based on key performance indicators: OEE per machine, machine group, and production line, production volume, unit counts, scrap rates, machine utilization, and more.
Analyze quarterly and annual results. With Selfbits, make better decisions and strengthen your company’s competitive position.
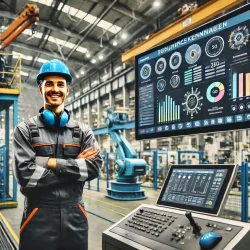
Shopfloor Signage
Use displays in your production or planning boards on your shop floor:
Department-relevant KPIs such as OEE, unit counts, scrap rates, and machine utilization are visible to all employees.
This creates transparency and boosts motivation and productivity within your workforce.
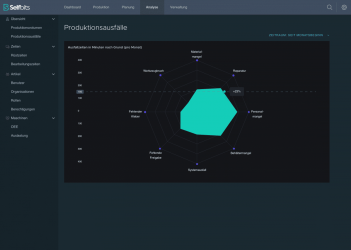
Andon & Disruption Management
Combine automated data acquisition from your machines with manual feedback on disruption causes via tablets.
Selfbits enables you to conduct regular evaluations and analyses of your most critical disruption reasons. Derive performance optimization measures and discuss them with your maintenance and quality assurance teams at your shop floor board.
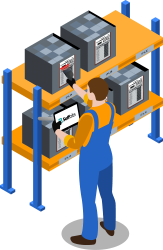
Batch tracking
With Selfbits, you always know where your intermediate products are. Barcodes, RFID, NFC tags, and more help you track the flow of your intermediate products and materials on an item basis.
Digitally assign your materials to the corresponding machines on-site. Document material consumption per order and item, while inventory levels synchronize directly with your ERP system.
With Selfbits, you can optimize waiting, storage, transport, and processing times, increasing the efficiency and profitability of your production.
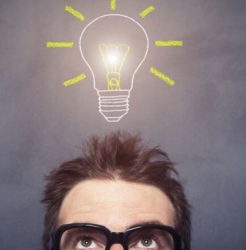
Do you have a specific use case?
Every company has its own unique challenges and requirements.
Custom development projects are pioneering work and bring great joy to our developers. These are the projects that position your company in a unique market situation.
Simply share your ideas with our consultants. Our developers are excited to turn your special requests into reality.
Would you like to learn more in a personal consultation?We are happy to assist you.Simply book your initial consultation with one of our experts now.
(Duration: approximately 2 minutes)