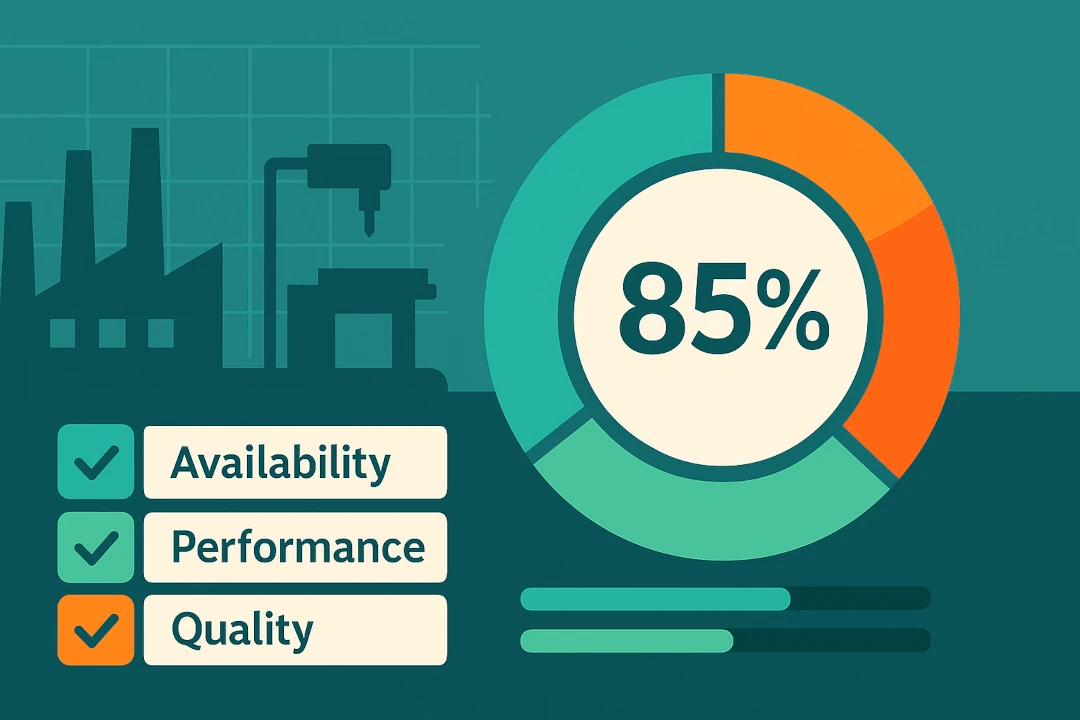
Availability in OEE calculation
Availability is one of the three factors used to calculate OEE. Below, we show how it is defined and calculated.
Availability is one of the three factors used to calculate OEE. Below, we show how it is defined and calculated.
Discover MTConnect, the open communication standard for collecting, transmitting, and analyzing machine data in production.
An MES (Manufacturing Execution System) is a software system used in the manufacturing industry to monitor, control, and optimize production in real-time.
Retrofitting involves adding sensors and connectivity components to existing machines. This enables MDA.
OPC UA offers a uniform data model and flexible transport options for securely networking devices from different manufacturers.
Modbus is an open industrial communication protocol from 1979 that easily connects devices such as sensors, drives, and control systems.
The Overall Equipment Effectiveness (OEE) refers to a production-related metric for determining the value creation of a facility.
Digitalization is revolutionizing the plastics industry: From additive manufacturing to machine data acquisition, networked processes enable greater efficiency, better quality, and faster time-to-market. OPC UA-based data interfaces create seamless integration of production facilities into the ERP/MES environment and lay the foundation for data-driven quality management and continuous optimization.
Digital shop floor management uses real-time data from MES and MDC/ODC, replacing manual collection and delivering data-driven process improvement.
5S is a systematic approach to optimizing the working environment. It supports productivity in a company by securing lasting cleanliness and order in all corporate divisions.
Operational data collection in production refers to the collection, recording, and evaluation of data that comes directly from the production process. These data can include information such as machine run times, downtimes, production quantities, quality parameters, and material consumption.
MDA transforms production and downtime into meaningful key performance indicators and provides the basis for real-time OEE optimizations. This turns data into measurable added value.
Andon is a visual management method and part of the Toyota Production System. In Japanese, the term “Andon” means (paper) lamp. With classic traffic lights and monitors (“boards”) in production, the Andon method forms a visual control system for the production status.
Poka Yoke, which means “avoid unfortunate mistakes” in Japanese, is a process design principle aimed at avoiding errors.
Value Stream Mapping (VSM) is a method for visualising manufacturing processes—specifically, their entire value stream — so they can be analysed and optimised.
Value stream management is the capture, control and planning of production and material flows in manufacturing — together with the associated flows of information.
Value stream design aims to eliminate the causes of waste uncovered during the value stream analysis by developing a future-state process.
Increase the efficiency of your production by identifying and eliminating the 7 wastes of lean manufacturing in your production process.
Data security encompasses every measure aimed at protecting all types of company-owned data. Find out more here.
Andon is a visual management method and part of the Toyota Production System. In Japanese, the term “Andon” means (paper) lamp. With classic traffic lights and monitors (“boards”) in production, the Andon method forms a visual control system for the production status.
Availability is one of the three factors used to calculate OEE. Below, we show how it is defined and calculated.
Poka Yoke, which means “avoid unfortunate mistakes” in Japanese, is a process design principle aimed at avoiding errors.
Value Stream Mapping (VSM) is a method for visualising manufacturing processes—specifically, their entire value stream — so they can be analysed and optimised.
An ERP system is a software solution for controlling business processes across every functional area. It ensures that corporate resources such as capital, personnel and material are provided on time and in line with demand, so that value creation remains efficient and company operations are continually optimised. The aim is to ensure an efficient value creation process and a continuously optimised management of business and operational processes.
Value stream management is the capture, control and planning of production and material flows in manufacturing — together with the associated flows of information.
Value stream design aims to eliminate the causes of waste uncovered during the value stream analysis by developing a future-state process.
Discover MTConnect, the open communication standard for collecting, transmitting, and analyzing machine data in production.
An MES (Manufacturing Execution System) is a software system used in the manufacturing industry to monitor, control, and optimize production in real-time.
Retrofitting involves adding sensors and connectivity components to existing machines. This enables MDA.
OPC UA offers a uniform data model and flexible transport options for securely networking devices from different manufacturers.
Modbus is an open industrial communication protocol from 1979 that easily connects devices such as sensors, drives, and control systems.
The Overall Equipment Effectiveness (OEE) refers to a production-related metric for determining the value creation of a facility.
Digitalization is revolutionizing the plastics industry: From additive manufacturing to machine data acquisition, networked processes enable greater efficiency, better quality, and faster time-to-market. OPC UA-based data interfaces create seamless integration of production facilities into the ERP/MES environment and lay the foundation for data-driven quality management and continuous optimization.
Digital shop floor management uses real-time data from MES and MDC/ODC, replacing manual collection and delivering data-driven process improvement.
5S is a systematic approach to optimizing the working environment. It supports productivity in a company by securing lasting cleanliness and order in all corporate divisions.
Operational data collection in production refers to the collection, recording, and evaluation of data that comes directly from the production process. These data can include information such as machine run times, downtimes, production quantities, quality parameters, and material consumption.
MDA transforms production and downtime into meaningful key performance indicators and provides the basis for real-time OEE optimizations. This turns data into measurable added value.
Increase the efficiency of your production by identifying and eliminating the 7 wastes of lean manufacturing in your production process.
The term overall equipment efficiency is often mistakenly used instead of overall equipment effectiveness. Overall Equipment Effectiveness (OEE) is a key performance indicator for the productivity of one or more machines and systems. It describes how close a machine operates to the ideal of continuous production at maximum performance without defects.
You need to load content from reCAPTCHA to submit the form. Please note that doing so will share data with third-party providers.
More InformationYou are currently viewing a placeholder content from Facebook. To access the actual content, click the button below. Please note that doing so will share data with third-party providers.
More InformationYou are currently viewing a placeholder content from Google Maps. To access the actual content, click the button below. Please note that doing so will share data with third-party providers.
More Information