OEE: Overall Equipment Efficiency or Overall Equipment Effectiveness?
The term overall equipment efficiency is often mistakenly used instead of overall equipment effectiveness.
Overall Equipment Effectiveness (OEE) is a key metric for the productivity of one or more machines and systems. It describes how close a machine operates to the ideal of continuous production at maximum performance without defects. OEE is composed of three factors: availability, performance and quality. It takes into account downtime (availability losses), reduced production speeds, minor stoppages, and quality defects (in the form of rejects and rework).
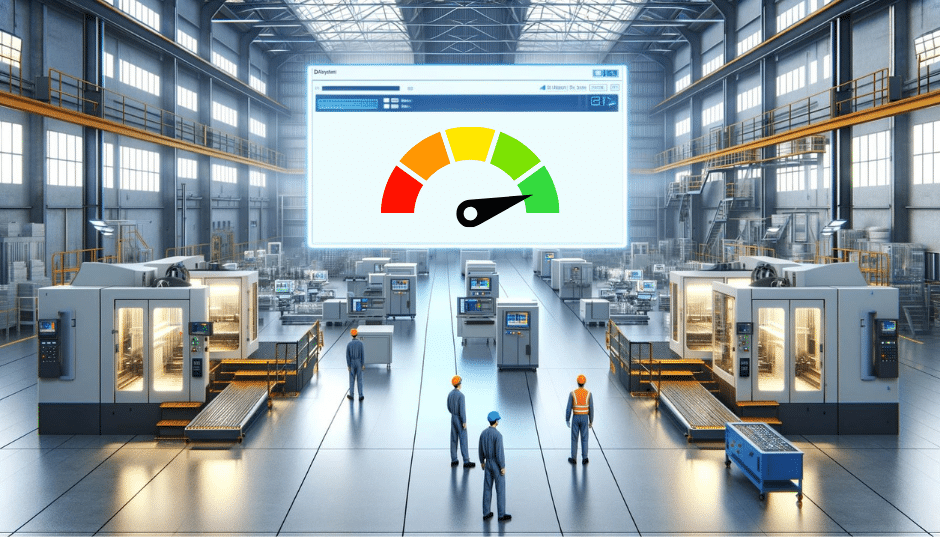
Efficiency and Effectiveness
Efficiency and effectiveness are often confused and related concepts, but they are fundamentally different.
Effectiveness deals with how well an action or process achieves its intended result. It often involves comparing the desired outcomes with the actual outcomes.
Efficiency, on the other hand, compares the achieved result with the resources expended. It focuses on how well resources are utilized to achieve a goal, aiming for minimal waste and optimal process performance.
Since OEE compares the actual output of good parts to the maximum possible output, it is a measure of effectiveness.
To determine the overall equipment efficiency of a machine, one would need to relate the output quantity to the costs or efforts associated with its operation. However, such an overall equipment efficiency offers limited insights given the typically high acquisition costs of machines. In most cases, the goal of process optimizations is to maximize the output of the existing machines.
Find out more
Learn more about OEE, what it indicates, and how it is calculated from availability, performance, and quality.