What is OPC UA?
OPC UA (Open Platform Communications Unified Architecture) is an open, platform-independent communication standard for transmitting process and machine data in industrial automation technology. It was developed to enable secure, reliable, and efficient data transmission between devices and applications.
OPC UA is a data transmission communication standard that allows for the standardization of communication protocols. It supports the integration of devices and applications from different manufacturers and facilitates data exchange between systems.
OPC UA is an evolution of the older OPC standard and offers improved security, reliability, and scalability. It is a significant standard in industrial automation technology and is commonly used in production environments, power supply systems, and process control systems.
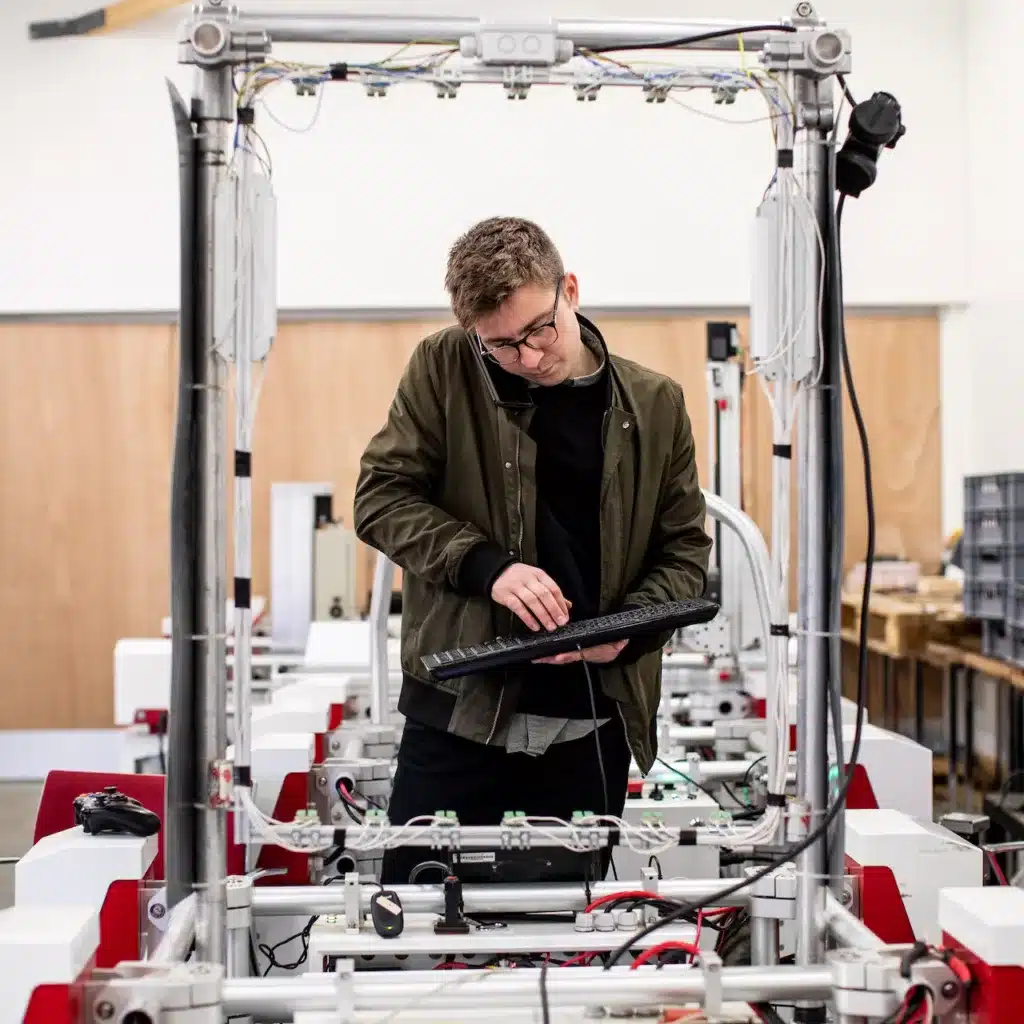
Operation of OPC UA
To understand the functioning of the communication standard, it is fundamental to know that the pure transport and the data format in OPC UA are largely separated.
The transport of data can be implemented via different protocols. For common transmission protocols, it is defined how the OPC UA data format is to be transmitted. This allows for various architectures to be realized. In addition to pub-sub mechanisms (transmission from one device to many others), the most common implementation is a client-server-based architecture. Here, communication occurs directly between an OPC UA client and an OPC UA server.
The server is a device or application that provides or receives data. The client is a device or application that queries data from the server or transfers data to it. During data transmission, the client must establish a connection with the server and should perform secure authentication. Once a connection is established, the client can query data from or transfer data to the server.
The data format is a particular feature of the standard. OPC UA uses a unified data model that describes the structure and meaning of the data being transmitted. This enables consistent processing and interpretation of the data by different devices and applications. OPC UA also offers high security by default, ensuring encrypted transmission of data and authentication of the devices and applications involved.
Overall, the standard enables reliable and secure data transmission in industrial automation systems, contributing to better integration and efficiency.
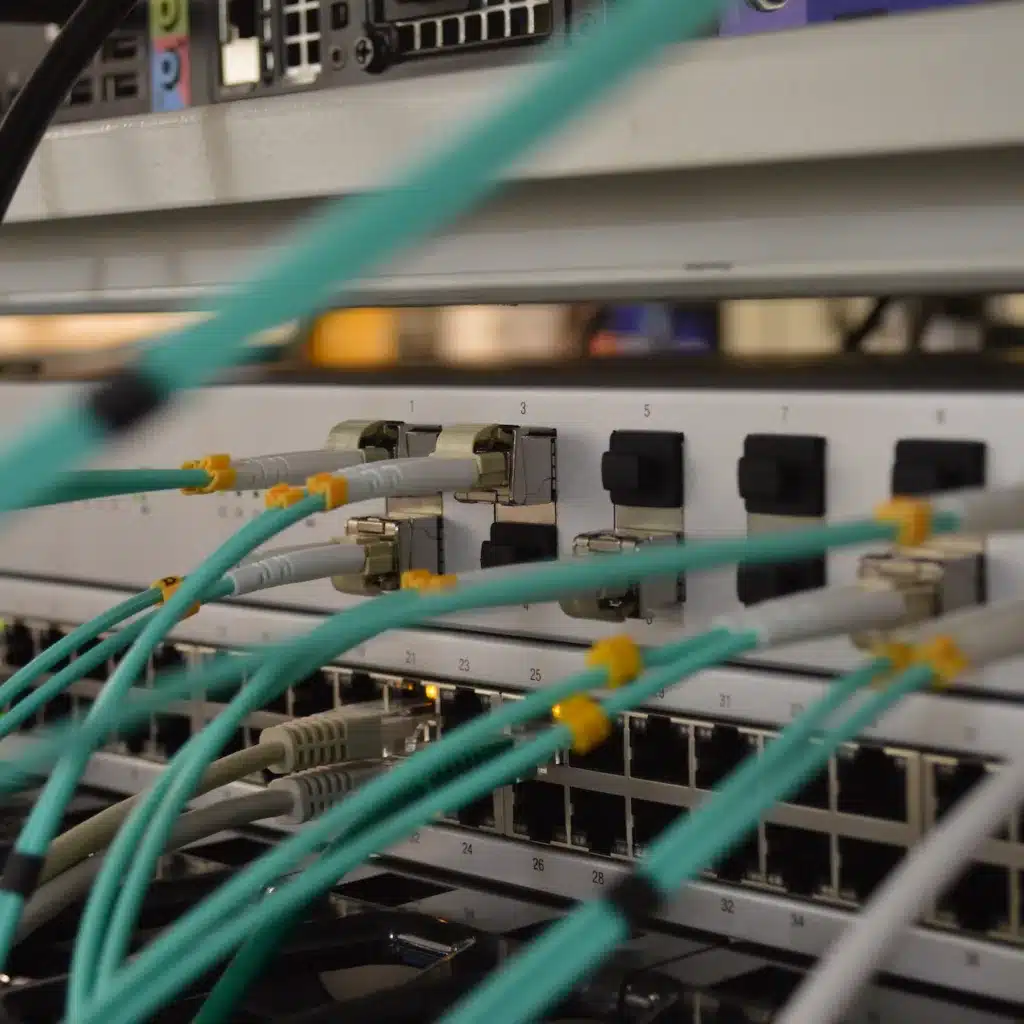
Relevance
OPC UA is strategically highly relevant because it represents a crucial step towards manufacturer-independent standardization of communication among automation technology components.
In automation technology, there are numerous manufacturer-specific protocols used for data transmission and control commands. Here are some examples:
1. MODBUS: An open communication protocol commonly used in industrial automation systems. Developed in 1979, it is one of the most widely used protocols in automation technology.
2. PROFINET: A protocol for industrial networks developed by Siemens and the PROFIBUS User Organization. It is frequently used in automation technology and mechanical engineering.
3. EtherCAT: A high-performance Ethernet-based protocol designed for automation technology. It is often used in applications requiring high data rates.
4. CANopen: A communication protocol developed for data transmission in embedded systems and automation technology. It is an open protocol developed by Bosch and maintained by the CAN in Automation (CiA) user organization.
5. DeviceNet: A protocol for data transmission in automation technology developed by Allen-Bradley. It is commonly used in applications where devices and controllers need to be interconnected.
Often, manufacturer-specific protocols are only compatible with devices and applications from the same manufacturer. Therefore, integrated systems with devices from different manufacturers may encounter compatibility issues and require significant integration effort. OPC UA was developed to address these challenges by providing a unified communication interface for devices and applications from different manufacturers.
OPC UA affects not only automation engineers
You should consider this communication standard if you are in a role that involves the transmission, collection, or analysis of data in industrial automation technology. This particularly applies to:
System Integrators: As a system integrator, you are responsible for integrating devices and applications from different manufacturers into a unified system. OPC UA can help simplify these integration tasks by providing a uniform communication interface.
Automation Engineers: As an automation engineer, you are responsible for configuring and monitoring automation systems. OPC UA can help you transfer data more reliably and securely into higher-level automation systems.
Developers: As a developer, you are responsible for developing applications used in industrial automation. OPC UA can help you integrate your applications more easily and securely by providing a unified communication interface.
IT Managers: As an IT manager, you are responsible for monitoring and securing IT systems. The communication standard can help you transfer data more reliably and securely in your automation systems and enable better monitoring and control of the systems.
Purchasers: To ensure future-proof procurement, you should ensure that your supplier guarantees compatibility with OPC UA for new investments in machinery and equipment. Otherwise, you may incur additional costs for integration with other OT (e.g. SCADA control systems) or IT systems (e.g. MES) in a few years.
CEOs: At a strategic level, OPC UA is a key component for driving development towards Industry 4.0. In many cases, OPC UA compatibility is a prerequisite for strategic initiatives and projects in automation and MES.
Overall, you should consider OPC UA if you are in a role that involves data transmission in industrial automation technology. OPC UA provides a unified communication interface that helps you transfer data more reliably and securely and simplifies your integration and monitoring tasks.
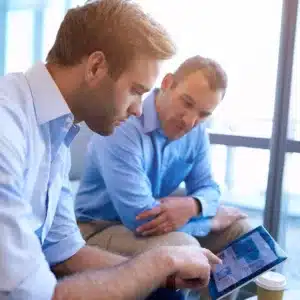
Do you have any questions about the communication standard?
Get in touch with us – we’re happy to speak with you for free and without obligation about your questions and your use case.
Case Study
To connect a machine to an OPC UA system, the following steps need to be taken:
1. Install an OPC UA server: An OPC UA server must be installed on the machine to provide its data to an OPC UA client, such as one from a Manufacturing Execution System (MES). This can be done by either the machine manufacturer or a developer/system integrator.
2. Configure the OPC UA server: The OPC UA server needs to be configured to establish the connection to the machine and the OPC UA client. Information such as the IP address and port number must be entered during configuration.
3. Establish a connection: After configuration, a connection between the OPC UA server and the OPC UA client must be established. This can be done using a common network connection such as Ethernet.
4. Monitor and control the machine: Once the connection is established, the system can monitor and control the machine using the OPC UA client. Data is sent from the machine to the OPC UA server and then forwarded to the OPC UA client for processing.
5. Integrate applications: Finally, a variety of applications can be integrated with OPC UA clients to read and process the data. Interfaces to SCADA software or an ERP system, for example, can be established.
In summary, OPC UA enables the easy and standardized connection of machines to a monitoring and control system.
DO YOU NEED FURTHER INFORMATION?
Feel free to contact us – we are happy to speak with you free of charge and without obligation about your questions and your specific use case.