Warum Industrie 4.0?
Industrie 4.0 bietet ein gewaltiges Potential für Produktivitätssteigerung. Auf dieser Seite wollen wir zeigen, welche Möglichkeiten es gibt, dieses Potential effektiv in der eigenen Fertigung zu nutzen. Dafür liefern wir Erklärungen zu Begriffen der Digitalisierung, zu technologischen Grundlagen und zur konkreten Anwendung.
Der Begriff "Industrie 4.0"
Industrie 4.0 ist erstmals 2011 als Sammelbegriff für den Einzug von Informations- und Kommunikationstechnologie in die diskrete Fertigung aufgetaucht. Er leitet sich aus den bisherigen industriellen Revolutionen und der in der Software-Entwicklung üblichen Versionierung ab.
Die erste industrielle Revolution erfolgte mit der Erfindung der Dampfmaschine im 18. Jahrhundert. Mithilfe der dampfbetriebenen Arbeits- und Kraftmaschinen war eine erste wirkliche Industrialisierung möglich geworden.
Die Fließ- und Förderbänder und die elektrische Energie ermöglichten ab dem Jahr 1870 die industrielle, arbeitsteilige Massenfertigung — die zweite industrielle Revolution.
Mit dem Einzug von Elektronik und Informations- und Kommunikationstechnologie in die Produktion wurde die bis heute andauernde dritte industrielle Revolution eingeläutet. Die Automatisierung schreitet in der Produktion immer weiter voran. Mithilfe von computergestützter Logistik wie Just-in-time-Lieferungen und optimierter Produktionsabläufe sind moderne, variantenreiche Serienproduktionen möglich geworden.
Die vierte industrielle Revolution bezeichnet die vollständige, echtzeitfähige Vernetzung von Menschen, Maschinen, Produkten und Werkstücken. Der Fokus liegt dabei zunächst auf der Produktion. Mit dem Einsatz von Big Data können Prognosen über den Produktionsverlauf getroffen, Störungen frühzeitig erkannt und der Produktionsablauf weiter optimiert werden.
Letztlich soll die Vernetzung aber über den gesamten Produktlebenszyklus vollzogen werden. Durch die so gewonnene Transparenz und Kommunikation ergeben sich verbesserte Produkte oder auch völlig neue Geschäftsmodelle, die die Kundenbedürfnisse zielgerichtet erfüllen.
Was macht Industrie 4.0 aus?
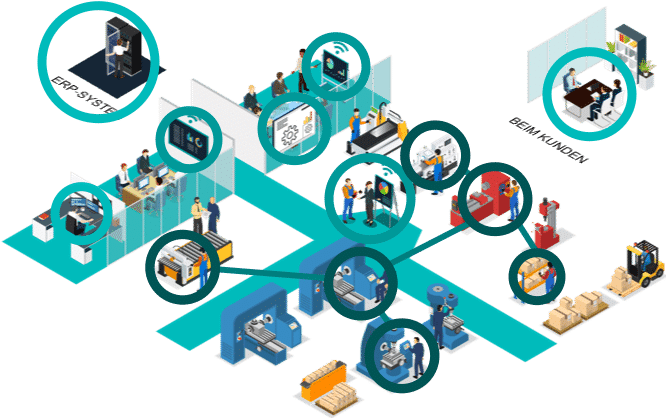
Zentrale Paradigmen der Industrie 4.0
Die Verbindung der unternehmenseigenen IT-Infrastruktur in eine festgelegte Hierarchie mit standardisierten Schnittstellen ist die vertikale Integration. Die horizontale Integration bezeichnet die Verknüpfung mit den IT-Systemen der Kunden, Lieferanten, externen Dienstleistern und weiteren. Zusammen ergibt sich so ein ganzheitliches IT-System, dass alle Geschäftsvorfälle intern, wie extern
Dezentrale Intelligenz beschreibt die Fähigkeit des Maschinenparks relevante Produktionsdaten wie z.B. Bestände oder Produktionsparameter an ein dezentrales Steuerungssystem weiterzuleiten.
Die dezentrale Steuerung ist der Gegenentwurf zu den ortsgebundenen und statischen SPS-Steuerungen. Industrial Internet of Things Lösungen und Cloud-Dienste ermöglichen eine geografisch verteilte flexible Steuerung.
Beim durchgängigen digitalen Engineering werden alle Prozesse im Unternehmen, von der Entwicklung bis zur Fertigung, als ganzheitliches System betrachtet. Ziel ist es ein vollständiges digitales Abbild des Unternehmen zu schaffen. Das verspricht aufgrund der gewonnenen Transparenz Produktivitätsgewinne und eine einfachere Optimierung.
Cyber-physische Produktionssysteme bezeichnen das Gesamtwerk aus Maschinenpark, Sensoren und Aktoren zusammen mit der integrierten Informations- und Kommunikationstechnologie.
Steigender Wettbewerbsdruck und Differenzierungsbedürfnisse sind Treiber für Weiterentwicklungen. Ersatzprodukte oder disruptive Veränderungen des Marktumfeldes durch neue Geschäftsmodelle verlangen es, weitere Optimierungspotentiale aufzudecken und zu nutzen. Gleichzeitig treten neue, vielfältige Kundenbedürfnisse auf, die zu neuen Varianten und steigenden Komplexitätskosten führen. Die Industrie 4.0 erkennt diese Unbeständigkeit und Veränderlichkeit als Realität von Unternehmen im 21. Jahrhundert an. Basierend auf integrierten Systemen liefert sie Antworten für Unternehmen in diesem Umfeld.
Lean Production und ihre Prinzipien haben in den 90ern zu einem erheblichen Effizienzgewinn in der Produktion geführt. Die konsequente Weiterentwicklung von Pull-Mechanismen, Just-in-Time und Qualitätssensibilisierung (wie z.B. Six Sigma) haben es ermöglicht, diese Produktivitätsgewinne inzwischen in nahezu allen Unternehmensbereichen zu realisieren.
Die heutigen, kurzen Produktlebenszyklen und der Wettbewerbsdruck führen zu der Suche nach weiteren Effizienzgewinnen, die sich mit Lean nicht mehr erreichen lassen. Erst mit dem Einsatz von moderner Informations- und Kommunikationstechnologie wird die Variantenvielfalt heutiger Produkte und die Optimierung auf Losgröße 1 für Unternehmen beherrschbar.
Dann speichern intelligente Werkstücke Informationen über ihre Verarbeitung und Verwendung. Gleichzeitig verfügen sie über eine Internetverbindung mit der sie Updates erhalten, Nutzungsdaten übermitteln können und Wartungsintervalle individuell regeln können. Die einzelnen Fertigungsschritte mit ihren Parametern werden über Industrial Ethernet an den vernetzten Maschinenpark gesendet. Dieser sendet die realisierten Fertigungsparameter, Produktionsmengen und weitere Rückmeldedaten an die dezentrale Steuerung zurück.
Daraus entsteht in der Industrie 4.0 ein ganzheitliches System aus Produkten, Geschäftsprozessen und hochwertigen Dienstleistungen, die neue Geschäftsmodelle ermöglichen und Produkte sinnvoll erweitern.
Der Mensch nimmt in der Industrie 4.0 primär die Rolle der Steuerungs- und Entscheidungsinstanz ein. Er ist über Augmented Reality und weitere Mensch-Maschine-Schnittstellen in den Produktions- und Steuerungsprozess eingebunden.
Enabler für die Industrie 4.0 und warum sie bisher noch nicht Einzug gehalten hat
Wesentlicher Treiber für die Umsetzung von Industrie 4.0 ist die heutige Verfügbarkeit von Kommunikations- und Informationstechnologie. Kostengünstige Sensorik, verknüpfte Systeme und Netzwerktechnik wie Industrial Ethernet machen es überhaupt erst möglich, Datenerhebung in der Produktion und Maschine-zu-Maschine-Kommunikation (M2M-Kommunikation) wirtschaftlich zu betreiben. Erst mit modernen Datensystemen, hohen Übertragungsgeschwindigkeiten und geeigneten IT-Architekturen ist es technologisch möglich, die Komplexität in der diskreten Fertigung abzubilden und dezentral zu steuern.
Mit der breiten und kostengünstigen Verfügbarkeit dieser Technologien ist die kundenindividuelle Massenfertigung (Mass-Customization) auch in der diskreten Fertigung von Mittelständlern möglich geworden.
Dafür nötig ist aber die Weiterentwicklung der Produktion hin zur intelligenten Fabrik. In dieser werden die Lehren und Prinzipien moderner Produktionssysteme wie dem Lean Management befolgt und mithilfe der Informations- und Kommunikationstechnologie weitere Produktivitätsgewinne geschaffen.
Smart Factory
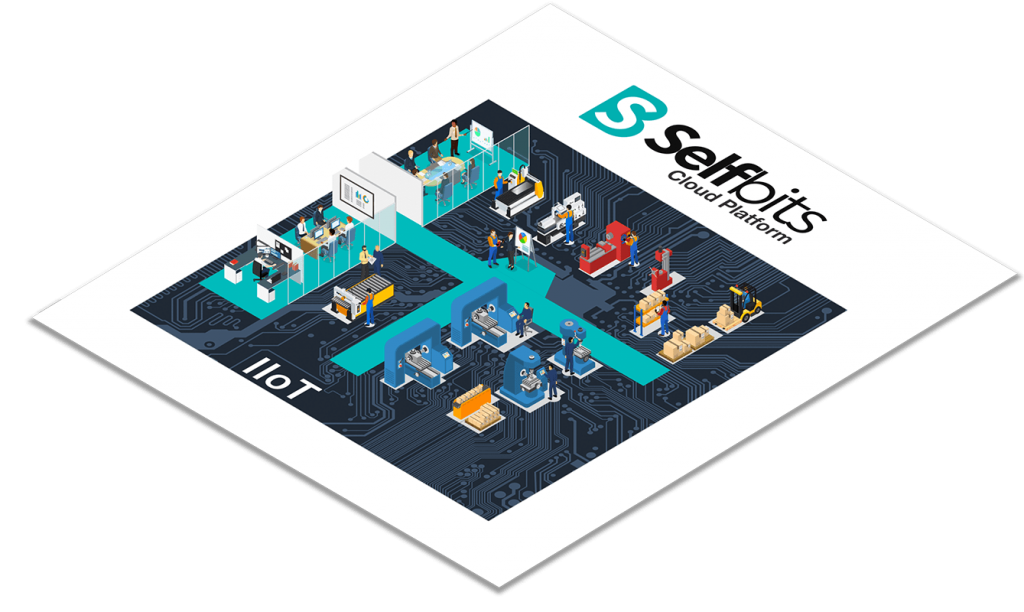
Das Zielbild der Industrie 4.0 ist die intelligente Fabrik — Smart Factory. Dort tauschen Maschinen, Werkstücke und Menschen Informationen direkt untereinander aus. Die Informationen wie Produktionsmengen, Rückmeldedaten und Produktionsparameter werden dezentral zur Verfügung gestellt. Aktuelle Aufträge von Kunden, Lieferdaten der Lieferanten sind in dem System eingepflegt und können genutzt werden, um den Produktionablauf zu optimieren. Es werden automatisch Nachbestellungen ausgelöst, Aufträge eingeplant und über Liefertermine informiert. Der Mensch erfüllt in diesem System primär eine Kontroll- und Entscheidungsinstanz. Er überwacht die Fertigung und steuert nur bei Störungen oder anderen Ereignissen nach. Was in der Prozessindustrie dank abgeschlossener Systeme und vollständig kontrollierbarer Variablen bereits üblich ist soll nun auch Einzug in die diskrete Fertigung nehmen.
Wir freuen uns auf Ihre Kontaktaufnahme!
Selfbits steht für sinnvolle und maßgeschneiderte Softwarelösungen im Bereich IoT und Industrie 4.0.
Wir ermöglichen unseren Kunden eine detaillierte Datenerfassung und Transparenz in der eigenen Produktion.
Die tiefgehenden Einblicke und daraus resultierenden Erkenntnisse werden von unseren Kunden genutzt, um ihre Produktionseffizienz nachhaltig zu erhöhen.
Als „Die Forschungsuniversität in der Helmholtz-Gemeinschaft“ schafft und vermittelt das Karlsruher Institut für Technologie (KIT) Wissen für Gesellschaft und Umwelt.
Selfbits begann als Spin-off am KIT. Wir sind auch weiterhin eng mit dem KIT, insbesondere dem Lehrstuhl von Prof. Weinhardt, der KIT Gründerschmiede und dem Innovations- und Relations-management (IRM) verbunden.
EXIST ist ein Förderprogramm des Bundesministeriums für Wirtschaft und Energie (BMWi).
Es unterstützt die Vorbereitung innovativer technologieorientierter und wissensbasierter Gründungsvorhaben von Studierenden, Absolventinnen und Absolventen sowie Wissenschaftlerinnen und Wissenschaftlern. Selfbits wurde von 2015 bis 2016 durch EXIST gefördert.