Maschinenstörung in der Produktion
Maschinenstörungen die einen Maschinenstillstand und damit eine Unterbrechung im Produktionsprozess bewirken, sind jedem der im produzierenden Umfeld tätig ist bekannt. Auch die negativen Konsequenzen solcher Störungen sind bekannt. Dabei geht es nicht nur um die direkt sichtbaren Probleme wie eine reduzierte Ausbringung, eine erhöhte Zykluszeit, Ausschuss, Materialverschwendungen und eine im Ergebnis schlechtere Auslastung der Maschine. Insbesondere die mittelbaren Effekte, nämlich eine reduzierte Liefertreue, höhere Kosten und unzufriedene Kunden sind maßgebliche Gründe sich mit dem Thema Störungsmanagement eingehend zu befassen.
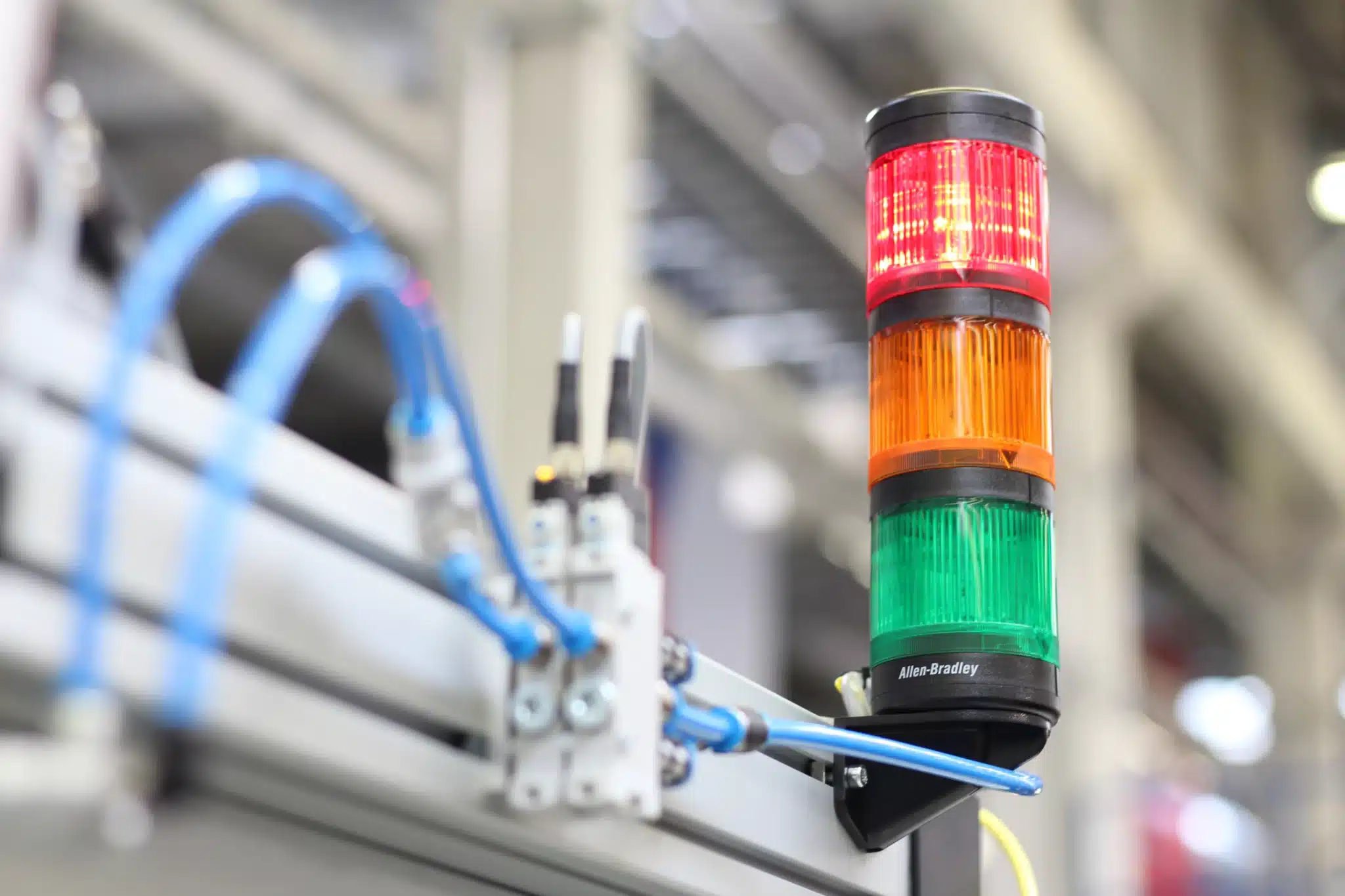
Störungsmanagement schafft Transparenz
Ohne Störungsmanagement gehen wertvolle Informationen darüber, wann eine technische Störung auftrat (Früh-/Spät-/Tagschicht), bei welchem Teil, Artikel oder Werkzeug sie oder bei welchem Fertigungsschritt sie auftrat verloren. Diese Informationen sind meist nur den Mitarbeitern die an der Maschine tätig sind bekannt und werden, sofern sie nicht notiert werden vergessen. Jedoch können diese Informationen dabei helfen die zugrundeliegende systematische Ursache der Störung zu identifizieren und Maßnahmen zur Abstellung abzuleiten.
Der erste Schritt: papierbasierte Erfassung und anschließende Auswertung in Excel
Viele Unternehmen versuchen im ersten Schritt die systematische Erfassung von Störungen, Stillständen und den jeweiligen Gründen papierbasiert vorzunehmen. Zur weiteren Auswertung wird in weiteren Schritten eine systematische Überführung der erfassten Störungen und Stillstände inklusiver potenzieller Fehlercodes und Störgründe in Excel vorgenommen. Dies erfolgt im besten Fall täglich, indem z.B. eine adminstrative Kraft die Werte von Papier in Excel für die weitere Analyse überträgt. Die Störungen können und z.B. nach absoluter oder relativer Häufigkeit pro Störgrund ausgewertet werden, oder nach der durchschnittlichen Dauer. Dadurch lassen sich dann Prioritäten zur Maßnahmenentwicklung festsetzen um die schwerwiegendsten und akutesten Probleme abzustellen.
Zentrale Vorteile dieses Ansatzes sind die Möglichkeit einer schnellen Einführung, die einfache Möglichkeit per Arbeitsanweisung die Art der Erfassung anzupassen und die Möglichkeit schnell erste Ergebnisse zu erhalten. Excel gibt weiterhin eine gewisse Flexibilität die es einem größeren Personenkreis ermöglicht mit den Daten eigene Auswertungen durchzuführen.
Die Nachteile sind jedoch mannigfaltig. Beginnend bei der Erfassung zeigt sich in der Praxis, dass die Erfassung von technischen Störungen im „Eifer des Gefechts“ gerne mal vergessen wird. Die Maschine und damit der Prozess steht. In dieser Situation ist die oberste Prämisse, die Maschine und den Prozess wieder zum Laufen zu bekommen. Entsprechend, wird ggf. der Meister oder die Instandhaltung informiert und man versucht gemeinsam das Problem möglichst schnell einuzugrenzen und zu lösen. Für eine detaillierte Erfassung bleibt oftmals keine Zeit. Sofern eine Dokumentation der Störung überhaupt erfolgt, sind die zugehörigen Zeiten, d.h. Beginn und Ende der Störung wenig zuverlässig, da diese im Nachhinen grob geschätzt werden und nicht zum jeweiligen Eintritt der Störung dokumentiert werden.
Die zeitliche Ungenauigkeit ist bis zu einem gewissen Grad akzeptabel, allerdings wird sie spätestens bei systematisch auftretenden Mikrostörungen zum Problem, denn diese werden in diesem Zuge oftmals überhaupt nicht erfasst. Unter Mikrostörungen versteht man dabei kurzzeitige Prozessunterbrechungen, z.B. von wenigen Sekunden, die für sich genommen unkritisch wirken, bedingt durch Ihre Häufigkeit in der Summe aber signifikante Auswirkungen auf Gesamtverfügbarkeit der Anlage bzw. der Maschine haben.

Exkurs: Auswirkung von Mikrostörungen
Um die Relevanz zu verdeutlichen, betrachten wir nachfolgendes Rechenbeispiel. Nehmen wir eine Unterbrechung von 15 Sekunden, die pro Stunde 10 Mal auftritt und damit zu einer Gesamtstörungszeit von 2,5 Minuten pro Betriebsstunde führt. Bei Drei-Schichtbetrieb summieren sich diese Unterbrechungen pro Tag auf 60 Minuten, bei Ein-Schichtbetrieb auf 20 Minuten. Im Jahr kommen wir damit bei 365 angenommenen Arbeitstagen im Dreischichtbetrieb auf sage und schreibe 25900 Minuten oder 45,63 Tage im Ein-Schichtbetrieb auf 7300 Minuten oder 15,21 Tage.
Wir verlieren somit durch die augenscheinlich „unkritischen“ 15-sekündigen Unterbrechungen 4,2 % unser theoretischen Maschinenkapazität. Hier ist daher dringend Handlungsbedarf geboten!
Störgrundklassen erleichtern die Analyse
Auch die Klassifikation von Störungen, also die Einteilung in vordefinierte „Gründe“, trägt maßgeblich zum Erfolg einer Erfassung bei. Überlässt man in einer papierbasierten Erfassung den Mitarbeitern die Art und Weise wie sie Störungen beschreiben so sieht man sich in der späteren Analyse mit unstrukturierten und im schlimmsten Fall nicht auswertbaren Daten konfrontiert.
Beispielsweise erfasst Kollege 1 für eine Störung als Grund „Maschinenstörung Werkzeug verschmutzt“ und Kollege 2 „Werkzeug funktioniert nicht“. Ohne Rücksprache mit den Kollegen wird es für denjenigen der die Daten auswerten möchte nicht möglich sein sicher zu entscheiden ob die Art der Störung bei beiden Kollegen gleichartig oder unterschiedlich war. Selbst falls sich dies mit dem Ergebnis klären lässt, dass es sich um identische Störungen handelt ist eine sinnvolle Gruppierung, z.B. in Excel ohne zusätzliche Arbeit nicht möglich, da sich die Texte unterscheiden. Beide Effekte führen dazu, dass die Aussagekraft der Daten sinkt, die Analyse fast unmöglich wird, und das Vorhaben häufig schnell wieder aufgegeben wird, bzw. sich der Nutzen nur auf die jeweils aktuellste Dokumentation pro Schicht beschränkt. Eine sinnvolle langfristige Analyse wird aufgrund der mangelhaften Datenqualität im Regelfall nicht möglich sein.
Eine Maßnahme zur Verbesserung dieser Situation kann sein, Formblätter zu erzeugen auf denen Kategorien oder Störgründe vorgegeben sind, die die Freitextbeschreibung ergänzen. Die Kollegen werden dabei angewiesen mindestens die Kategorie auszuwählen und zusätzlich weitere Informationen zur Störung und zu deren Behebung zu ergänzen. Dieses Vorgehen hat den massiven Vorteil, dass in einer späteren Analyse nach den ausgewählten Kategorien geclustert werden kann. Oftmals ist dies bereits ausreichend um die größten und drängendsten Probleme (z.B. mangelhafte Werkzeugreinigung) zu identifizieren und Maßnahmen zur Abstellung einzuleiten.
Es geht auch anders: digitale Erfassung und Analyse
Wer die oben genannten Probleme umgehen und ohne Mehraufwand systematisch Störungsmanagement betreiben möchte setzt auf eine digitale Lösung. Auch hier gibt es mehrere „Ausbaustufen“ die wir nachfolgend erläutern.
Erfassung und Analyse von Störungen über digitale Formulare oder "no-code"/"low-code" Apps
Eine einfache Möglichkeit mit einem digitalen Störungsmanagement zu beginnen bieten auf den ersten Blick Formularlösungen wie Microsoft Forms / Sharepoint, Google Forms oder no-code App Builder. Ebenfalls beliebt sind einfache proprietäre Datenbanklösungen wie Microsoft Access oder Filemaker Server. Aus diesen können die Daten dann über Excel oder BI Lösungen wie PowerBI, Tableau oder ähnliche ausgewertet werden.
Die vorgenannten Erfassungslösungen dienen dazu eine standardisierte Eingabemaske über Formularfelder zu erstellen, die dann entweder in ein Spreadsheet wie Excel oder direkt in eine relationale Datenbank (wie z.B. MySQL) zu speichern um sie anschließend auswerten zu können.
Vorteile eines solchen Ansatzes ist, dass er durch technikaffine und qualifizierte Mitarbeiter in Eigenregie durchgeführt werden kann und bis zu einem gewissen Punkt funktioniert.
Die Grenzen dieses Ansatzes werden jedoch oftmals schnell erreicht. Dazu zählen Probleme beim Berechtigungsmanagement (wer darf auf welche Daten zugreifen?) bei der Verknüpfung mit anderen Datenquellen (beispielsweise der Zuordnung zu ERP-Auftragsdaten). Wenn kein fachlich ausgebildets Personal mit belastbarem fachlichen Hintergrund im Bereich Anwendungsentwicklung und Datenbanken zur Verfügung steht können dadurch schlecht-integrierte Insellösungen entstehen die eine parallele Stammdatenstruktur schaffen. Das problematische dabei ist, dass dies den betroffenen Personen aufgrund des fehlenden Fachwissens häufig nicht bewusst ist und sich erst dadurch äußert, dass gewisse Anforderungen nicht mehr erfüllt werden können und das System „stagniert“. Es kann damit im bestehenden Zustand weiterverwendet werden, aber „mehr geht nicht“. Gleichzeitig sind die auf diese Weise selbst gebauten „Tools“ schon so fest in den Betriebsablauf integriert dass ein einfaches „abschalten“ auch nicht mehr funktioniert. Dies ist eine sehr unschöne, aber leider häufig anzutreffende Situation.
Erfassung und Analyse von Störungen über eine dedizierte MES Software mit BDE/MDE
Als derzeit nachhaltigste und zukunftssicherste Alternative bietet sich eine dedizierte professionelle Lösung zur Betriebsdatenerfassung (BDE) und Maschinendatenerfassung (MDE) an, die im besten Fall Teil eines integrierten MES-Systems ist. Eine solche Lösung wird im Regelfall die Daten soweit es möglich ist über Schnittstellen direkt aus den Maschinen extrahieren, z.B. per OPC-UA und über BDE Terminals die manuelle Rückmeldung von zusätzlichen Daten ermöglichen, die nur der Werker dem System mitgeben kann, wie beispielsweise getroffene Maßnahmen zur Problemlösung.
Vorteile von BDE/MDE und MES
Die zentralen Vorteile sind eine signifikant bessere Datenqualität als in anderen Ansätzen, da die Daten sekunden-exakt aus den Steuerungen extrahiert werden. Zudem kann über eine solche Software einfach und unkompliziert eine Einstellung von Störgrundkategorien vorgenommen werden, nach denen fortlaufend und über beliebige Zeithorizonte nach Häufigkeit und Dauer ausgewertet werden kann um Maßnahmen abzuleiten. Das klassische Problem, nach der Einführung von Maßnahmen nicht zu wissen ob diese auch wirken, wird dadurch umgangen, dass für eine entsprechenden DMAIC-Prozess die entsprechenden Daten und Kennzahlen fortlaufend erhoben werden, d.h. es ist möglich Kennzahlveränderungen unmittelbar nachzuvollziehen und daraus abzuleiten, ob eine Maßnahme den gewünschten Effekt erzielt, z.B. eine Reduktion der Störfälle durch Werkzeugverschmutzung um 25%.

Umgang mit alten Maschinen
Selbst wenn an einzelnen Maschinen keine direkte Datenerfassung möglich ist, z.B. weil die Maschine noch aus den 1980er Jahren stammt, können dort Daten erfasst werden. Möglich ist zum einen ein Retrofitting, das bedeutet die Nachrüstung von Sensorik zur Erfassung von Betriebszuständen. In diesem Fall ist dann genau wie bei vorhandener Schnittstelle eine automatische Datenerfassung, also MDE, möglich. Ist diese Option in extrem seltenen Fällen technisch nicht gangbar, oder nicht wirtschaftlich, so kann die Rückmeldung auf die Betriebsdatenerfassung beschränkt werden. In diesem Fall erfolgt die Rückmeldung manuell durch den Werker, aber in einem eng geführten Eingabeprozess, mit klar definierten Kategorien um Eingabefehler zu minimieren.
Öffnung weiterer Potenziale
Der zentrale Vorteil, die erfassten Daten fortlaufend und jederzeit auswerten zu können ist bei Verwendung eines MES mit BDE und/oder MDE jederzeit gegeben. Es ergeben sich daher neben dem reinen Störungsmanagment wirkungsvolle Möglichkeiten für den internen kontinuierlichen Verbesserungsprozess, z.B. die Darstellung auf digitalen Andon Boards und die Verwendung der Daten in täglichen Shopfloor Meetings.
Haben wir Ihr Interesse geweckt?
FAQ
Nein. Die Selfbits Manufacturing Suite lässt sich am ehesten mit einer integrierten BDE/MDE und PPS/MES Lösung vergleichen. Sie hat das Ziel, den Prozess von „Rampe-zu-Rampe“ im Sinne eines digitalen Zwillings entlang des Wertstroms möglichst detailliert abzubilden und alle relevanten Daten im Prozess zentral zu erfassen. Darauf aufbauend kann die Kernwertschöpfung optimiert und die zukünftige Produktion besser geplant werden. Stammdaten wie Artikel, Material und Maschinen werden über Schnittstellen aus dem ERP synchronisiert oder einmalig übertragen. Sämtliche buchhalterischen Prozesse finden weiterhin im ERP statt.
Ja. Alle gängigen ERP Systeme (SAP, ProAlpha, ABAS, Sage, Navision, Infor) bieten Schnittstellen um Daten zu extrahieren oder zurückzuführen. Gerne besprechen wir mit Ihnen Möglichkeiten zur Integration mit Ihrem bestehenden ERP.
Ja. Wir helfen gerne bei der Integration. Sprechen Sie uns einfach an.
Die Selfbits Manufacturing Suite bietet Schnittstellen über REST und GraphQL um auf Daten zuzugreifen. Dies erlaubt die eigenständige Entwicklung von Lösungen im Haus und die Integration mit anderer Software. Datenexporte nach Excel sind ebenfalls möglich.
Jein. Unser Standard Betriebsmodell sieht das Hosting in der sicheren Cloud von AWS in Frankfurt am Main vor. Wenn Sie zwingend eine On-Premise Lizenz benötigen nehmen Sie bitte Kontakt mit uns auf, dann finden wir gemeinsam eine Lösung.
Die Daten werden zentral in der AWS Cloud in Frankfurt am Main gespeichert und verarbeitet. Für jeden Kunden wir eine eigene VPC (Virtual Private Cloud) aufgesetzt, um die Sicherheit der Daten zu gewährleisten. Erfahren Sie mehr darüber in unserem Datenschutz und Datensicherheit Whitepaper.
Es ist kompliziert. Wir haben zu unserem eigenen Erstaunen in der Zusammenarbeit mit unseren Kunden festgestellt, dass Barcodes häufig deutlich günstiger und einfacher in der Handhabung sind als Lösungen mit NFC oder RFID. Die Auswahl der „Trägertechnologie“ ist letztlich immer abhängig von den Gegebenheiten in der Produktion. Setzen Sie große Behälter und automatisierte Handhabungstechnik ein, so geht die Tendenz zu RFID. Verwenden Sie kleine Behälter und gibt es Prozessschritte mit extremen externen Einflussfaktoren wie Temperatur oder Feuchtigkeit sind Barcodes häufig die bessere Option. Details besprechen wir gerne persönlich mit Ihnen.
Ja. Solange sich etwas mechanisch bewegt oder Strom fließt sind wir in der Lage mindestens rudimentäre Prozesssignale zu erfassen.
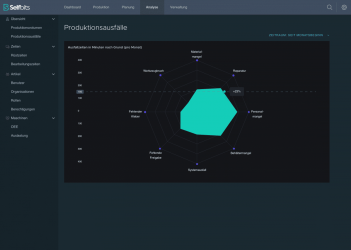
Störungsmanagement
Störungen werden entweder automatisch von der Maschine oder händisch per Tablet erfasst und inklusive Störgrund gespeichert. Im Falle einer Störung können so automatisch Mitarbeiter benachrichtigt werden. In der Weboberfläche können Störungen im Zeitablauf nach Dauer und Grund visualisiert werden.
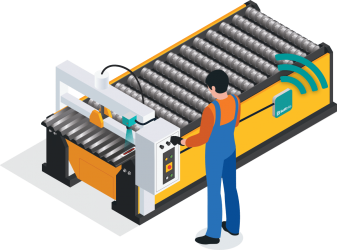
Maschinendatenerfassung
Mit Hilfe von flexiblen Hardwarelösungen helfen wir Ihnen dabei, relevante Maschinen- und Sensordaten fortlaufend artikel- und auftragsbezogen zu erfassen, zu speichern und für die Analyse bereitzustellen.
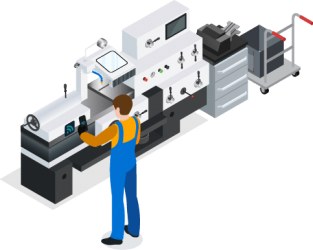
Betriebsdatenerfassung in Echtzeit
Nutzen Sie Tablets an Maschinen oder die Flexibilität von Smartphones um Rüstzeiten, Maschinenstillstandszeiten und -gründe sowie Gut- und Schlechtteile flexibel in Echtzeit zu erfassen.